Beat the Heat: Thermal Management Solutions
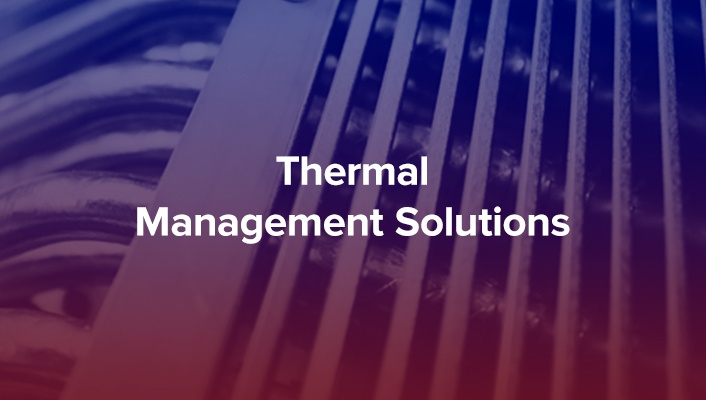
Temperature is a crucial variable in many industrial and mechanical processes. Diverse applications require integrated thermal management solutions to help remove excess heat. When it comes to product design and engineering, it’s essential to understand the key concepts and the fundamentals of managing temperature in sensitive systems.
What Is Thermal Management?
Thermal management is a wide-ranging term that involves the creation, movement, and removal of heat in a specified system. It’s how engineers and designers can control the temperature of a system with technology.
Thermal management systems use principles of thermodynamics and heat transfer, which include conduction, convection, and radiation, to increase or decrease the temperature distribution of said technology.
From buildings to electrical devices to the human body, heat transfer can help regulate temperatures for diverse applications by moving heat from one place to another.
The Importance of Thermal Management
All circuits and devices generate some form of excess heat during use. Thermal management helps mitigate extremely high temperatures, relative to each device’s temperature threshold, that can cause critical components to overheat and deteriorate.
Most people have experienced the lag of a computer or smartphone when it gets too hot. If these problems extend to life-supporting machines, such as aircraft or electronic components in vehicles or military equipment, the downtime caused by overheating can be catastrophic.
Thermal management in these electronics aims to close the gap between the system’s specifications and the requirements of its industry. As products become more electrified, digitally connected, and higher-powered, thermal management becomes even more essential to enhance product design and manufacturability by controlling the heat they generate during use.
Keeping Your Devices at Safe Operating Temps
Designers can use different working fluids and heat transfer technology to move heat away from electronic devices in a few ways:
- Air cooling: Vapor is a traditional and easy-to-employ form of a working fluid, but modern cooling demands often surpass the capability of air cooling systems.
- Liquid cooling: Liquid systems offer sufficient capabilities for many applications. They can be combined with other types of cooling to create a system-level solution.
- Two-phase cooling: These systems use a combination of vapor and liquid fluid types for an innovative cooling solution that can meet strict temperature specifications.
Cooling is just one strategy that engineers can use when creating thermal management solutions for their applications. Complex systems may require several methods to protect electronics against failure and ensure they meet industry demands for faster performance.
Heating or Cooling
All devices have a minimum and maximum operating temperature. Outside of these thresholds, their regular operation becomes potentially compromised. Adding or removing heat through thermal management ensures these systems operate within their optimal temperature range.
Heat Removal
Without proper thermal management, devices may become too hot to touch and risk the product’s user experience. An example of this is touch-safe devices for medical procedures. Heat removal helps transfer the thermal energy away from the heat-generating source.
Cycling
Cycling provides both heating and cooling for a system using defined temperature extremes. It’s effective in systems that may need a uniform temperature over a specified length, volume, or area.
Temperature Homogenization
Electronics that run closer to their upper or lower limits may have a shorter service life before they degrade, making operations unsafe and inefficient. Temperature homogenization strategies help mitigate the risk of unwanted temperature fluctuations that put the system at risk of failure.
When Thermal Management Fails
Keeping devices cool with the proper thermal management system helps improve their longevity and reliability. Even more importantly, system reliability helps ensure safety.
The resulting downtime and potential hazards caused by system overheating are unacceptable for medical, defense, aerospace, and transportation applications where lives could be at stake.
How Does Thermal Management Work?
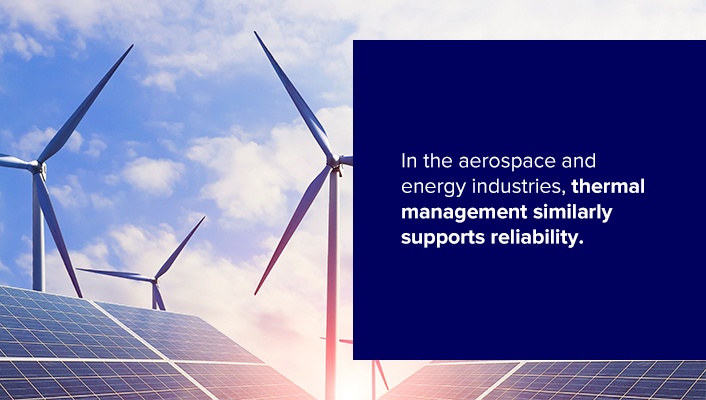
Effective thermal management is essential for maintaining the performance and longevity of electronic systems across industries like aerospace and energy. By carefully selecting heat transfer components, materials, and system configurations, engineers can regulate temperature and ensure reliable operation.
Thermal management can be achieved through a specific heat transfer component on an electrical device known as a thermal management system. They use defined borders to dictate whether they can transfer energy, work, and mass as expected.
A system’s required specifications describe the effectiveness of these transfers in changing the system’s temperature or temperature distribution. These parameters can be simplified or made more complex with multiple components, different materials, varying sizes, combining fluid types, and stable or transient behaviors.
Additionally, the material used to produce each component is crucial for the thermal management in electronic devices. Because of its naturally superior high-temperature resistance and stability, mica is preferred in applications that require suitable insulation for vital electronic components.
In the aerospace and energy industries, thermal management supports reliability. Various forms of working fluids, heat transfer technologies, and other system parameters regulate heat differently for diverse applications.
The system’s heat capacity determines the amount of heat needed to raise its energy level. Regardless of how that heat enters the system — through heat transfer or created by an internal source — the resulting increase in thermal energy causes the temperature to rise.
Thermal management systems control how much heat is stored internally and when it needs to be discharged through heat transfer processes, such as conduction, convection, or radiation, to achieve your desired results.
Conduction
Conduction is heat transfer through physical contact between objects at different temperatures. When solid materials touch, the cooler material naturally draws the thermal energy away from the warmer device. This heat transfer process can move a large amount of heat and requires the least surface area, making it effective for many thermal management applications.
Convection
Convection involves the movement of air molecules to redistribute thermal energy. The force of attraction leads cooler, denser molecules to sink and warmer, less-dense molecules to rise. As cooler air passes by the warm device via natural or forced convection, excess heat is drawn up and away from the component with the air current.
Most thermal management solutions rely heavily on convection to regulate temperature. Passive solutions use only natural air forces like buoyancy to move the air molecules. Active solutions use fans, pumps, or blowers (forced convection processes) to redistribute and speed up the movement of heat.
Both convection types are effective methods of heat transfer, but active solutions can increase the amount of energy that can be transferred.
Radiation
Radiation is when heat transfer occurs away from objects in the form of electromagnetic waves. As charged particles interact and move, they generate coupled electric and magnetic fields. This process converts the kinetic energy of heat into electromagnetic energy, which emits from the source and spreads out as it goes.
Because it falls between the visible and infrared parts of the electromagnetic spectrum, radiation often propagates through space via visible or non-visible light.
Engineers use radiation for industries that require a vacuum, where conduction and convection won’t work. Unless the application must rely on radiation because particles are absent, engineers may disregard this mode of heat transfer in their calculation due to its limited effectiveness.
Choosing the Right Thermal Management System: Applications for Advanced Thermal Management
As end-user demands for faster performance and more power-dense products continue to rise, thermal management of electronics has become essential to support safety and efficiency across industries and applications.
Systems required for devices across varying industries have unique thermal management needs, so different cooling methods are required to address those demands.
1. Industrial Applications
Many industries and markets require thermal management to prevent deteriorated performance of their processes and operations. Engineers can provide solutions for a wide range of industrial applications, including:
- Control cabinet cooling of FPGAs, power diodes, thyristors, and others electronics
- Motor drives
- Calibration furnaces
2. Medical Applications
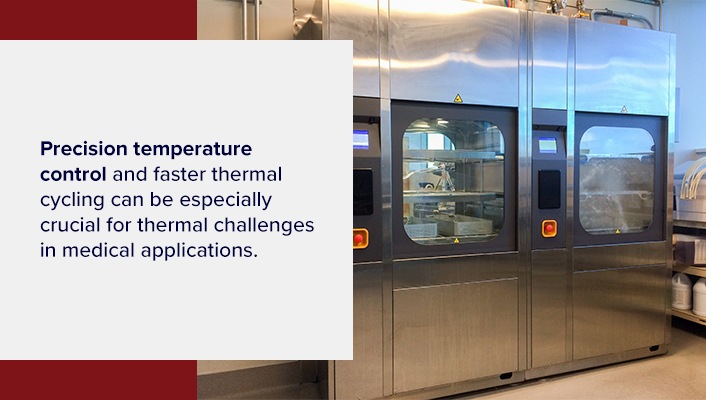
Thermal management solutions can serve many diverse needs in the medical industry. Different cooling strategies can reduce device operating temperatures, resulting in higher efficiency, an increased duty cycle, and enhanced safety for patient contacting surfaces.
Precision temperature control and faster thermal cycling can be especially crucial for thermal challenges in medical applications such as:
- Laser diodes
- Test and measurement equipment
- Sample transportation containers
- Diagnostic equipment
- Surgical devices
- Medical Imaging systems
- PCR devices
3. Transportation Applications
Active and passive thermal management technologies can be used to meet the increasing demands of various transport industries, including automotive, rail, electric vehicles (EVs), and EV chargers.
Thermal management for transportation applications must include proper insulation for maximized battery life, ventilation, and provisions for extreme weather. Heat-dissipating and heat-spreading technologies can help engineers address thermal challenges in areas such as:
- EV charging stations
- Power electronics
- IGBT and MOSFET
- Brake and suspension cooling systems
- Railway signal control
4. Defense, Aviation and Aerospace Applications
The thermal management of electronic systems is a limiting factor for many applications in the military, aviation, and aerospace industries. Common thermal solutions may no longer meet their increasingly challenging weight, temperature, and general operating requirements.
Innovative, system-level thermal management solutions are needed to increase component reliability in these harsh environments. Military vehicles, military and commercial aircraft, spacecraft, satellites, and other aerospace equipment and vehicles use thermal management systems to solve challenges such as:
- Vibration, shock, and sustained maneuvers
- Battery thermal management
- Large-magnitude acceleration
- Wide temperature ranges
- Altitude and direction changes
Top 3 Thermal Management Challenges
In addition to initial temperature concerns, thermal engineers may encounter added challenges when selecting a thermal management solution for a specified system. As electronic systems become more sophisticated and deliver higher speeds, rising power requirements can result in potential challenges like heat-spreading restrictions, convection limitations, and higher ambient temperatures.
1. Heat-Spreading Restrictions
The thermal conductivity (k) of a given heat-spreading material is directly related to its thermal management effectiveness. As electronic systems generate higher operating temperatures, materials that were once adequate to conduct heat away from the device may no longer hold up.
This is especially true in high-heat flux devices or concentrated arrays of heat sources. The quickest solution is to select a material with a higher thermal conductivity. Today’s top heat-spreading materials include:
- Copper
- Silver
- Diamond
- Graphite
- Heat pipes
- Vapor chambers
However, these materials often come with some trades offs:
- Copper has high thermal conductivity but is heavy, which can be undesirable for many applications.
- Silver, diamond, and pyrolytic graphite have terrific high thermal conductivities but are too expensive for most commercial products.
- Other materials may need more layers or increased thickness to obtain adequate thermal conductivity, creating weight or size challenges.
Generally, passive, two-phase devices like heat pipes and vapor chambers are often chosen for enhanced thermal conductivity without significant weight or cost impact.
2. Convection Limitation
Many thermal management technologies utilize convection to regulate system temperatures, so any challenges related to convection limitations can be detrimental.
Check if the air-side temperature rise is too large to meet system or component temperature requirements. Then, consider the following aspects of the thermal management system to circumvent this challenge:
- Increase the physical size of the heat sink or radiator: The larger the size, the lower the delta T you can achieve.
- Limitations: weight and geometric considerations.
- Increase the airflow: Higher air velocity generally leads to a lower delta T.
- Limitations: fan reliability and noise considerations.
- Optimize design elements: Change the design of components such as fin pitch and thickness with a system-level design solution.
- Improve fin efficiency: Create uniform temperature with advanced heat transfer. Consider how different material properties could help improve heat transfer, too.
3. High Ambient Temperatures
The ambient temperatures require sub-ambient cooling. However, high ambient temperatures pose a unique cooling challenge that eliminates all passive or “above ambient” cooling options.
For low-power cooling options, Peltier modules are the top consideration. Peltier coolers are semiconductor components that act as heat pumps. When the cold side of the module is attached to a warm device, the Peltier cooler can transfer thermal energy away from the device without many moving parts. ACT offers a variety of solutions for sealed sub-ambient, off-the-shelf options.
Benefits:
- Control temperatures with precision
- Reduced failure rates
- Minimal noise
- Can keep temperatures below the maximum limit independently (more than any other cooling system)
Considerations:
- Increased power consumption
- Active solution — adds more heat to the overall system
For higher power sub-ambient cooling needs, vapor compression cooling (VCC) is often considered. VCCs use a refrigerant and closed-loop vapor-compression cycle to cool the heat source to a temperature below the ambient air.
The basic components of the VCC cycle include the compressor, condenser, expansion valve, and evaporator.
Benefits:
- Can lift high heat loads
- Sealed solution
- Plug-and-play capabilities, which ensure fast and effective setup
- Door or wall mounting capabilities with minimal cabinet space needed
Partner With Advanced Cooling Technologies, Inc.
As a leading manufacturer of advanced thermal management solutions, we understand the specifications for various industries and are committed to helping our customers meet their unique requirements.
Our team specializes in custom two-phase heat transfer technology and thermal management products for diverse electronics cooling applications. Trust ACT to be your partner no matter where you are in the design cycle — from initial concept generation to prototyping.
